The Importance of Training
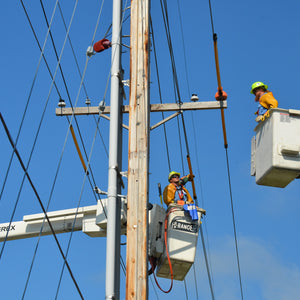
Training has been a subject of multiple articles on the Lug-All blog. We’ve covered a handful of different types of training, including emergency training, safety training, and equipment training. Why do we focus on the topic of training so often? Training is vitally important for completing any job safely and efficiently, and it is even more so in higher-risk professions.
When it comes to working safely, the two types of training that are most important are safety training and equipment training. When we talk about safety training, we’re typically talking about workers’ actions and behavior. It involves following safety protocols and standard operating procedures, using appropriate protective gear, avoiding risky behavior, etc.
When we talk about equipment training, we’re typically referring to the proper use of tools and equipment necessary for a job. Equipment training can refer to both the practical operating information for particular equipment—basic how-to-use information—and knowing what tools or equipment are the most appropriate for any given job or task.
Many linemen know the importance of training well. Most linemen attend extensive lineman training courses or dedicated lineman schools. These programs, often required to work for utilities, equip workers entering the field with the safety and equipment training necessary. However, training isn’t a once-and-done requirement. Both safety and equipment training can be ongoing, and both can change over time as equipment and safety procedures are updated.
Benefits
Whether you’re a lineman or a Lug-All user in one of the many other industries we serve, the benefits of comprehensive workplace training are multifaceted. Workers who have received appropriate workplace training can typically work more safely and more efficiently. For workers, this training can mean less strenuous work and a lower risk of becoming injured. For employers, it can mean improved productivity and fewer workers’ compensation cases.
Equipment training can also help improve the lifespan of your tools. Equipment might wear out prematurely or even break if used incorrectly. Ensuring tools are used correctly can keep repair and replacement costs down. Additionally, workers who use the right tools for different situations, and who use tools correctly, get the most benefit from those tools, once again improving productivity.
In any application in any profession, training is a key element. Proper training sets up workers to succeed at any job, which is good for everyone involved.